一、?發展與應用
所謂“超微粉體”,國內外目前對這一名詞尚無嚴格的界定。有人定義粒徑小于100um的為“超微粉體”,也有人定義粒徑小于1um的為“超微粉體”。但通常的習慣做法是小于500目(即30um)以下的粉體,即稱之為“超微粉體”。
固形物質經過超微粉碎后,使其處于微米甚至納米尺寸時,該物質的物理、化學特性都將發生極大的變化。
例如:TiO2,當其粒度為20?nm時可見光的遮蓋力最佳,可作為高檔油漆、油墨材料。粒徑減小到10~60?nm時,則具有透明性,強紫外線光的吸收能力,可作為高檔化妝品及透明涂料等。
??又如植物花粉,被譽為“微型營養寶庫”,對人體有優良的保健作用,但花粉的單體都具有堅硬的外殼,直接服用則無法被人體吸收。而經過超微粉碎,使花粉破壁,有效成分得以完全釋放,由此開發的花粉系列產品,可直接被人體所吸收。
??利用“超微粉體”的特異性能,在軍事上涂裝于飛機、艦船和坦克的表面,可制成隱身飛機、艦船和坦克,在航天領域,可制成耐高溫、高壓的輕型材料及新型燃料。
在化工、塑料、油漆、涂料等行業中,“超微粉體”可制成高強度、高附著力的高檔新產品。
在醫藥和醫療領域,將藥品制成“超微粉體”,經研究表明,可提高藥品的溶出度,減輕毒副作用,無論內服或外用,都能明顯提高療效。
總之,在我國從八、九十年代開始才逐步被越來越多研究部門和行業所重視。今后,必將在新材料、醫藥、日化、保健、化工、軍工、電子、航天等領域內取得全新的長足的發展。
?
二、氣流粉碎與分級
超微粉體的制備通常有物理和化學兩種方法。物理方法中,又可劃分為干法和濕法兩種。在化學方法中,又可分為氣相法、液相法等。
在物理方法中,干法超微粉碎又可分為球磨機、震動磨機、氣流粉碎機等,濕法超微粉碎機械中包括液流粉碎機、均質機等。在化學方法中,氣相法又包含真空蒸發法、氣相化學反應法、等離子體法等。在液相法中,主要有沉淀法、氧化加氫分解法、還原法、噴霧干燥法、冷凍干燥法等。
下面重點介紹物理方法中的氣流粉碎與分級機。氣流粉碎機屬于物理方法中干法粉碎類。
氣流超微粉碎機。目前,在工業上應用十分廣泛, 以其結構簡單、產品細、分布狹窄、純度高而享有盛名。
氣流超微粉碎機有以下幾種基類型:
(1)?水平圓盤式氣流粉碎機;
(2)?循環管式氣流粉碎機;
(3)?對噴式(逆向)氣流粉碎機;
(4)?撞擊板式(靶式)氣流粉碎機;
(5)?流化床式氣流粉碎機。
氣流粉碎機集多噴管技術、流化床技術和臥式分級技術于一身,實現了流場多元化及料層流態化與臥式分級化體系。此外,采用了氣體密封等多項新技術,可保證該機安全、高效、穩定地運行。
三、組成及工作原理。
氣流粉碎機組由空壓機、空氣凈化器系統、氣流粉碎機、分級機、旋風分離器、除塵器、排風機等組成。中、小型流化床式氣流超微粉碎機,通常將超音速氣流粉碎機、分級機、旋風分離器及除塵器、排風機等組合成一體機,可節省占地面積,有利于安裝、運輸和使用。
1.?粉碎原理
流化床式氣流超微粉碎機由料倉、螺桿加料器、進料室、粉碎室、旋風分離器、除塵器等組成。
首先,待粉碎物料由料倉經螺桿加料器,輸送至進料室,在重力作用下物料落入粉碎室。
粉碎室四周和設有相向排列的經特殊設計的高壓進氣噴嘴。經過凈化和干燥的壓縮空氣自噴嘴射出,形成超聲氣流。物料在高速氣流交點中心發生碰撞,瞬間內被粉碎。
經粉碎的粒子隨氣流上升至分級室,合格的粒子隨氣流進入旋風分離器,最終獲得所需產品,尾氣進入除塵器排出。
較大的顆粒在分級機作用下,重新回落粉碎室,再次被粉碎,直至獲得合格的產品。
2.氣流分級原理
在超細粉碎過程中,要想獲得數微米甚至更微細的粉體,采用普通的篩分方法是行不通的。因此本機在分級室內設置有渦輪式分級系統,這是利用離心力場的典型結構。
粉碎室內被粉碎的物料,受上升氣流的推動,在分級室臥式渦輪分級機的作用下,如果在渦輪旋轉斷面邊緣處有同一顆粒,此顆粒將受到離心力場兩種不同力的作用。即由渦輪旋轉而產生的離心慣性力F和氣流阻力R。
假設顆粒的粒徑為d、密度為δ、介質的密度為ρ、顆粒的切向速度為Ut、渦輪平均半徑為r、介質粘度為η、顆粒的徑向速度為Ur。這兩個力可分別用下列方程式表示:
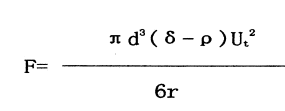
R=3πηd Ur
當顆粒較大時,所受離心力大于阻力,即F>R時,大顆粒沿渦輪切線方向飛向分級室器壁,然后返回粉碎室重新被粉碎。當離心力小于阻力,即F<R時,小顆粒隨上升氣流進入渦輪內部,經旋風分離器收集為合格產品。